Aufbau der Lernfabrik
Technologieschema
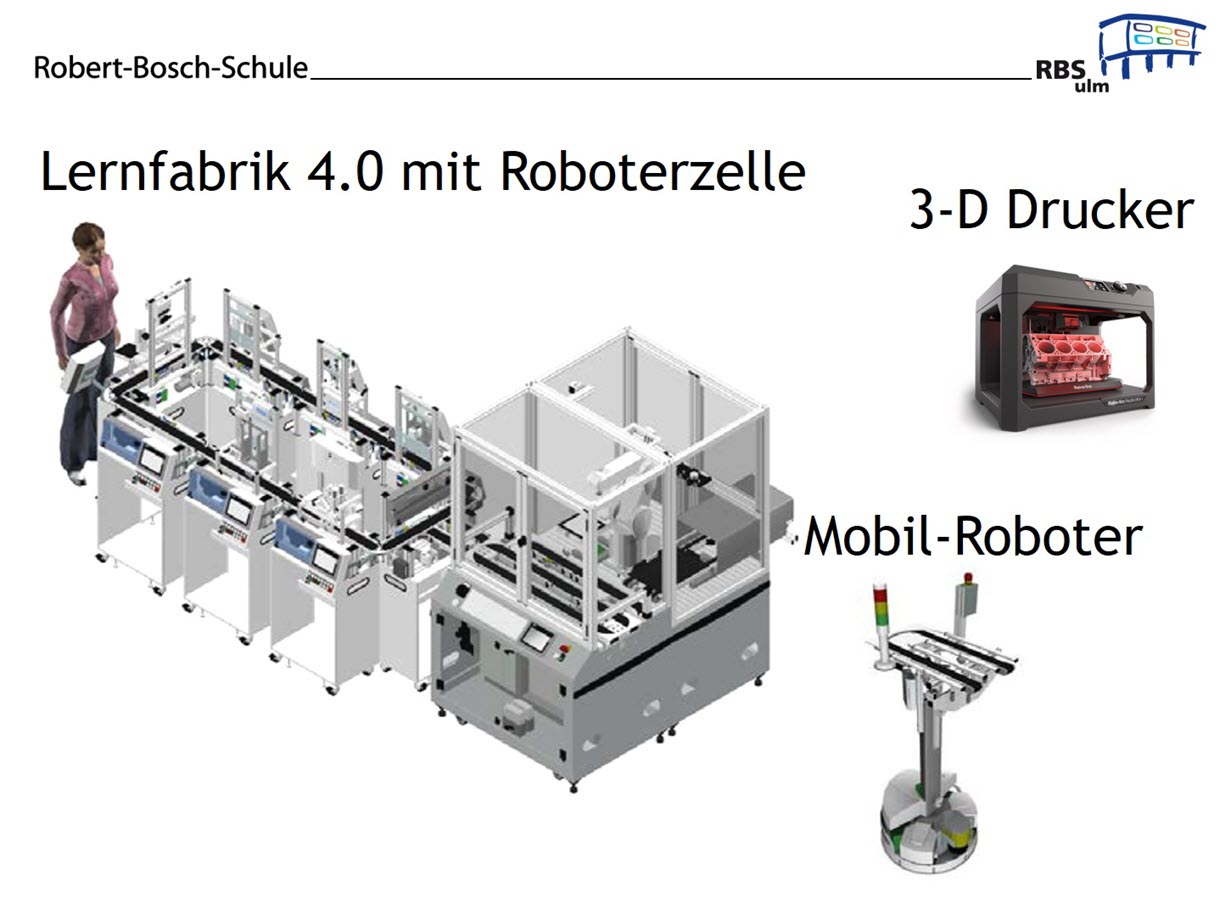
Bei der Lernfabrik 4.0 handelt es sich um ein modulares System, welches das Prinzip einer Handy-Montage realisiert.
Die Lernfabrik besteht aus 9 Palettentransfersystemen mit den nachfolgend beschriebenen Applikationsmodulen. Des weiteren ist eine Robotermontagezelle, ein fahrerloses Tranportsystem, ein 3D-Drucker sowie ein Handarbeitsplatz in das System integriert. Gesteuert wird die Lernfabrik über einen MES-Rechner der Firma FESTO. Eine Schnittstelle zu SAP4School, das an der Friedrich-List-Schule installiert ist, wird eingerichtet.
Der folgende Produktionsablauf wird an der Lernfabrik 4.0 realisiert:
Nach Start des Fertigungsauftrags am MES-Rechner erreicht ein leerer Werkstückträger das Stapelmagazin1, das zur Bevorratung und
Einschleusung der Unterschale dient, und eine Unterschale wird auf den Werkstückträger gelegt. Dann wird der
Werkstückträger zur nächsten Station gefördert, der Produktweiche. Der MES-Rechner entscheidet, ob der aktuelle
Werkstückträger weiter zur Bohrstation gefördert wird oder ob dieser zum Handarbeitsplatz tranportiert werden muss.
Ist ein Transport zum Handarbeitsplatz erforderlich, wird ein Transportauftrag an das fahrerlose Transportsystem (Robotino) gesendet. Der Robotino holt den Werkstückträger bei der Produktweiche ab und fördert diesen zum Handarbeitsplatz. Der Werkstückträger wird auf den Handarbeitsplatz übergeben. Ein Werker kann nun vom 3D-Drucker individuell gefertigte Inlays in die Unterschale des Handys einlegen. Ist dies erfolgt, gibt der Werker den Werkstückträger frei. Der Robotino holt diesen vom Handarbeitsplatz und transportiert ihn wieder zur Produktweiche.
Die Produktweiche fördert den Werkstückträger zur Bohrstation. Die Bohrstation dient zum variablen Bohren der Unterschale. Der MES-Rechner entscheidet ob und wieviele Löcher in die Unterschale gebohrt werden müssen. Die Bohrstation transportiert den Werkstückträger zur nächsten Produktweiche.
Bei dieser Produktweiche wird entschieden, ob eine Platine in die Unterschale eingelegt werden muss. Ist dies der Fall, wird der Werkstückträger zur Robotermontagezelle gefördert.
Die Robotermontagezelle besteht aus einem KUKA KR6 Industrieroboter, einem Kamerasystem, einem Magazin für Platinen, 3 Speicher
für Feinsicherungen sowie einem Greiferwechselsystem für drei Robotergreifer.
Über mehrere Förderstecken gelangt der Werkstückträger an einen Stopper. Hier entnimmt der Roboter die Unterschale vom
Werkstückträger. Der Roboter legt die Unterschale in den Erfassungsbereich eines Kamerasystems, das die korrekte Orientierung der
Unterschale überprüft. Danach wird die Unterschale in einer Montageaufnahme abgelegt. Als nächstes wird eine Platine in die
Unterschale eingelegt und mit Feinsicherungen bestückt. Dabei sind mehrere Greiferwechsel am Roboter nötig. Wurde die Unterschale
erfolgreich mit der Platine bestückt, wird diese wieder in den Werkstückträger gelegt. Danach wird der
Werkstückträger aus der Robotermontagezelle gefördert.
Die nächste Bearbeitungsstation ist das Stapelmagazin 2. Diese Station dient zum Bevorraten und Einschleusen der Oberschale, die hierzu auf die Unterschale gelegt wird. Ist dieser Vorgang abgeschlossen, wird der Werkstückträger zur Pressstation transportiert.
Bei der Pressstation handelt es sich um eine "Muskelpresse" zum Verpressen von Ober- und Unterschale mit variablem Anpressdruck. Den auftragsspezifischen Anpressdruck erhält die Presstation vom MES-Rechner. Wurden die beiden Schalen verpresst, wird der Werkstückträger zur Wendestation gefördert.
In der Wendestation wird entschieden, ob das Werkstück aus dem Wersktückträger entnommen und um 180° gewendet werden muss. Nach der Wendestation wird der Werkstückträger mit dem fertig montierten und korrekt orientierten Werkstück zur Handlingstation transportiert.
Die Handlingstation dient zur manuellen Werkstückausgabe. Hier wird das Werkstück mittels eines Greifers vom Werkstückträger abgenommen und je nach Auftrag des MES-Rechners auf ein linkes oder rechtes Leerlaufrollenband gelegt. Der Werker kann nun das fertig montierte Werkstück entnehmen – der Fertigungsauftrag ist somit beendet.
Hardwarekomponenten
9 Pallettentransfersysteme, Wersktückträgertransport, FESTO
2 Stapelmagazine, Bevorratung und Einschleusen der Ober- bzw.Unterschale,FESTO
1 Bohrstation , Variables Bohren der Unterschale, FESTO
1 Wendestation, Wenden des Werkstücks, FESTO
1 Robotermontagezelle mit KUKA KR6, Platinen auftragsspezifisch bestücken und in Unterschale einlegen, Bevorratung Platinen,
FESTO
1 Pressstation, Verpressen von Ober- und Unterschale mit variablem Anpressdruck, FESTO
1 Handlingstation, manuelle Werkstückausgabe, FESTO
1 Fahrerloses Transportsystem "Robotino", Werkstücktransport, FESTO
1 3D-Drucker "Replicator", Ausdruck von individuellen Inlays, Makerbot
1 MES- Rechner "MES4", Fertigungssteuerung, FESTO
Verwendete Software
Software, Beschreibung, Hersteller
TIA-Portal V15, Programmierung der SPS-Steuerungen, Siemens
MES4, Fertigungssteuerung, FESTO
KUKA System Software 8.5, Roboterprogrammierung, KUKA
SAP4School, ERP-System, SAP